2013-09-24
SPC控制图的基本原理(上)
关键词:SPC控制图
导语:SPC控制图是统计过程控制的灵魂工具,可以说统计过程控制的主要工作是由SPC控制图完成的。本文将通过上下篇幅介绍SPC控制图的基本原理,上篇主要介绍SPC控制图的形成,下篇主要介绍SPC控制图基本要素及使用等。
SPC控制图是由沃尔特•休哈特于1924年首先提出。他认为:在一切制造过程中所呈现出的波动有两个分量。第一个分量是过程内部引起的稳定分量(即偶然波动),第二个分量是可查明原因的间断波动(异常波动);那些可查明原因可用有效方法加以发现,并可被剔去,但偶然波动不会消失,除非改变基本过程;休哈特建议用正态分布N(μ,σ2)的概率特性界限μ±3σ(详情见下表)作为控制限来管理过程。休哈特认为基于3σ限的SPC控制图可以把偶然波动和异常波动区分开来。
界限μ±kσ
|
界限内的概率(%)
|
界限外的概率(%)
|
μ±0.67σ
|
50.00
|
50.00
|
μ±1σ
|
68.26
|
31.74
|
μ±1.96σ
|
95.00
|
5.00
|
μ±2σ
|
95.45
|
4.55
|
μ±2.58σ
|
99.00
|
1.00
|
μ±3σ
|
99.73
|
0.27
|
μ±4σ
|
99.9937
|
0.0063
|
正态分布N(μ,σ2)的概率特性
为了方便在现场使用和及时记录质量波动情况,休哈特还建议把正态分布图及控制限μ±3σ同时逆时针转90°。以横轴为时间或编号,以纵轴为过程参数(均值、标准差等),并在μ±3σ出引出两条水平线(用虚线表示),这样就形成一张SPC控制图(如下图)。
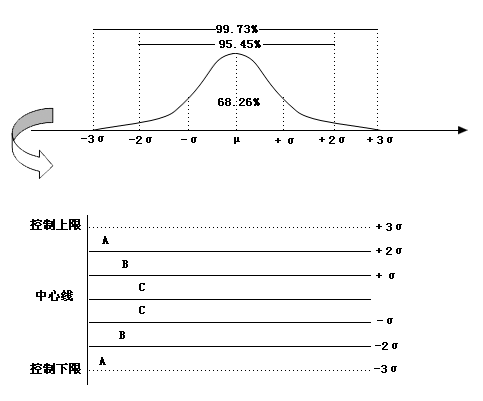
SPC控制图示意图
以上就是SPC控制图基本原理之控制图的形成,我们在使用SPC控制图时不仅要知其然还要知其所以然,这样才能正确地实施SPC,进行有效的过程质量管控。